Getting ready for winter season
Overview
Photos
November 21, 2013
Being a good manager, Gazprom always gets ready for winter well in advance. Therefore, “winter” already comes for us when the summer sun starts blazing through the window. In this photo essay we will give you an insight on how preparations for the forthcoming autumn-winter season are coming to an end through the example of our subsidiary company – Gazprom Transgaz Stavropol.
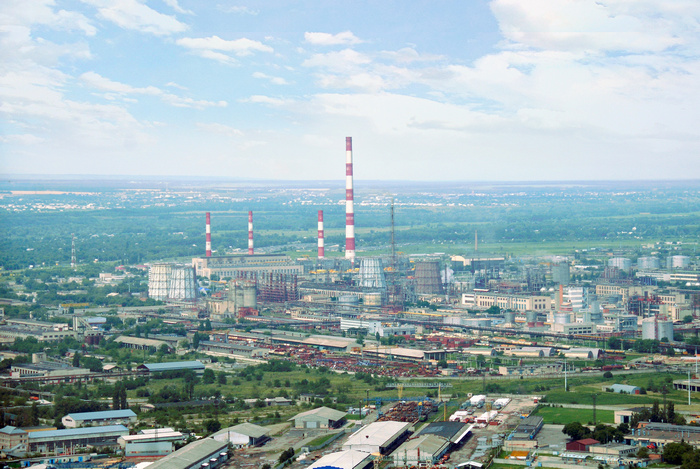
There are various types of gas consumers in southern Russia. For instance, the largest one is a chemical giant – Nevynnomyssky Azot.
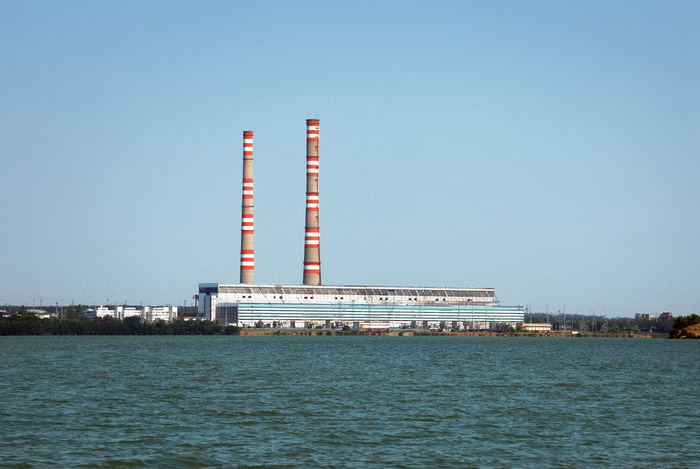
Others are smaller in scale, such as the Stavropol State District Power Plant which generates electricity from natural gas.
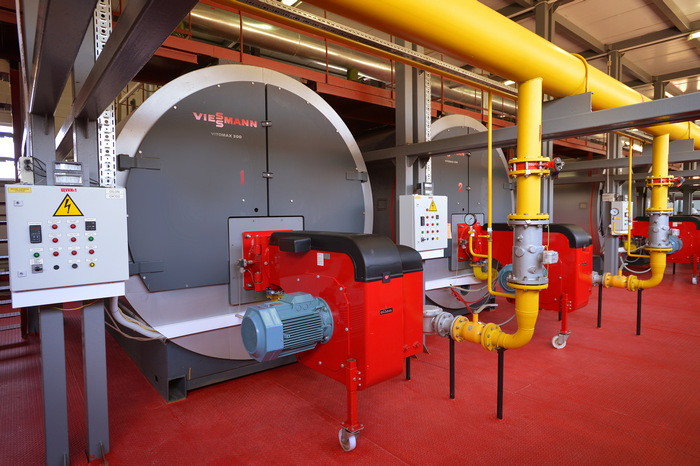
There are even much smaller, such as a boiler house in the village of Ryzdvyany.
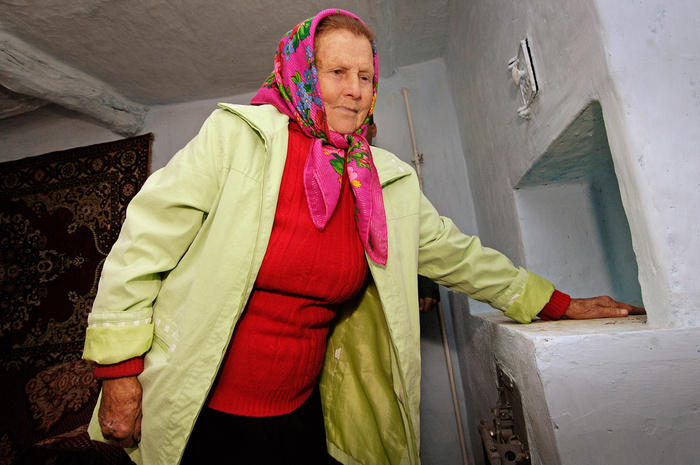
There is also an old lady named Anya from the small settlement of Krasnaya Balka, who doesn’t need fire wood, because the stove in her house is heated with gas.
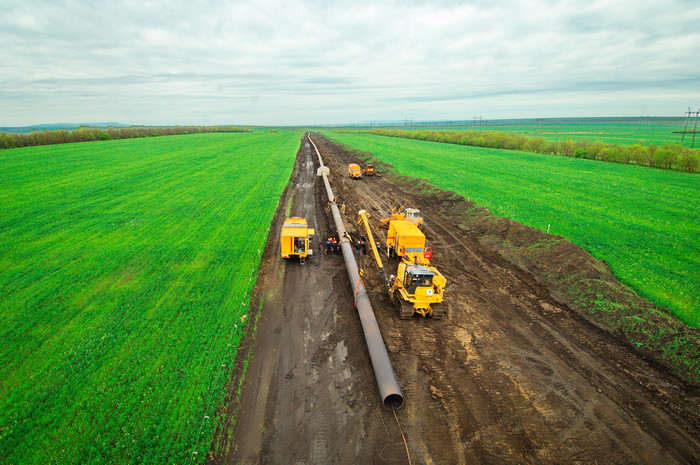
You certainly know that gas passes thousands of kilometers by long-distance gas pipelines before reaching the consumer. Therefore, it is extremely important for a gas transmission system to be always failsafe and reliable. Photo: overhaul and reinsulation of the Novopskov – Aksai – Mozdok gas pipeline is in full swing.
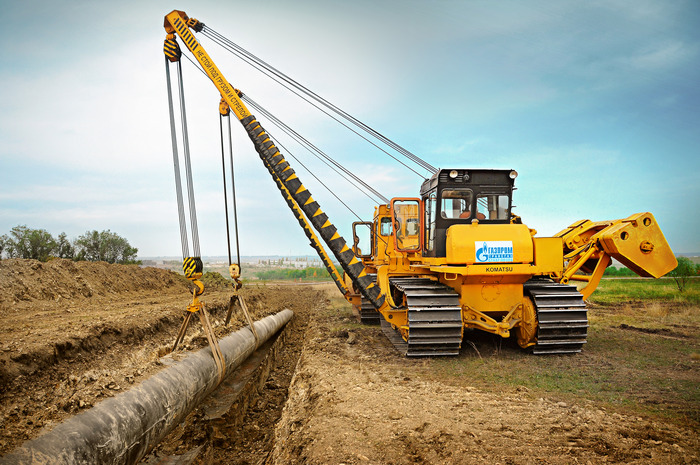
Gazprom Transgaz Stavropol operates one of the most developed gas infrastructures countrywide in the North Caucasian and Southern Federal Districts. The regional gas transmission system was one of the first built in the national gas industry. Therefore, Stavropol gas workers place high emphasis on capital repair, retrofit and upgrade of gas transmission facilities.
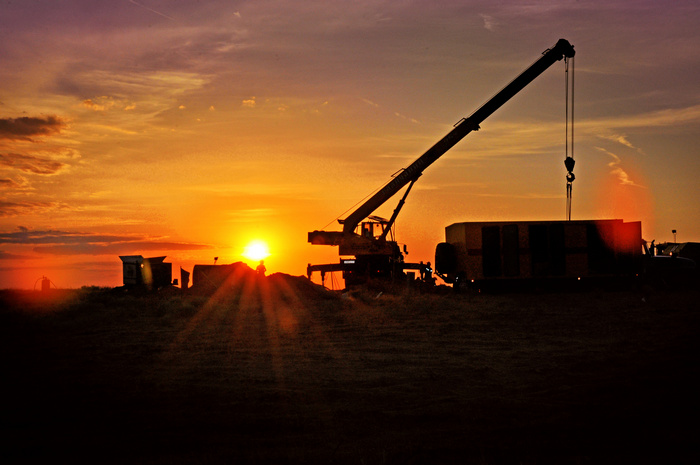
Gas workers are busy day and night to ensure that homes and apartments are warm and cosy, and industrial enterprises, housing & utility infrastructure, hospitals, schools and kindergartens function flawlessly.
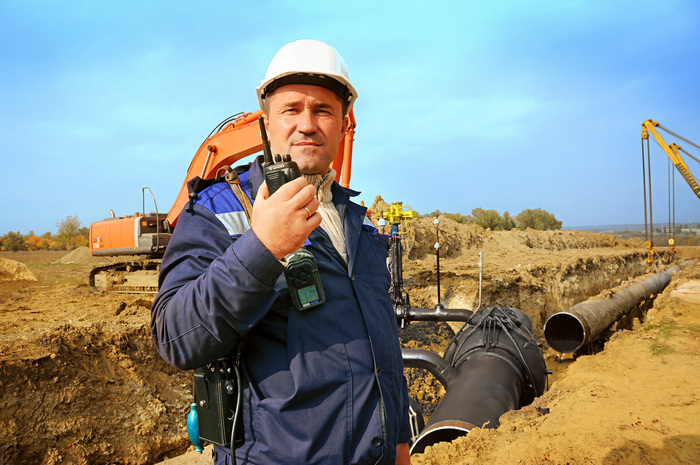
Large-scale operations usually engage a lot of structural units from various affiliates of Gazprom Transgaz Stavropol. That is why the concurrence of actions is crucial. Andrey Donets, head of a line pipe maintenance service, is in charge of hot works at a section of the Novopskov – Aksai – Mozdok gas pipeline (professionals call ‘hot works’ any work that involves welding or cutting with the use of fire-producing tools).
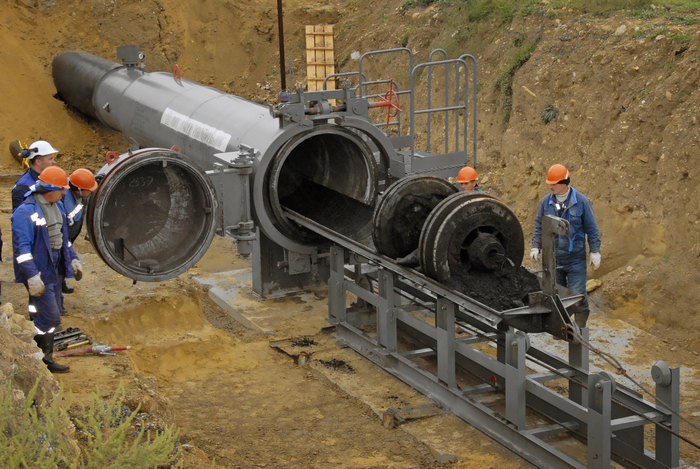
A gas pipeline must be in good repair to ensure uninterrupted gas supplies. To this end, regular in-line inspections take place. A special cleaning pig passes through the pipe and collects all the excess particles. Photo: a line pipe maintenance team from the Izobilnenskoye Gas Line Pipe Operation Center receiving the cleaning pig at a section of the Izobilnoye – Nevinnomyssk gas pipeline.
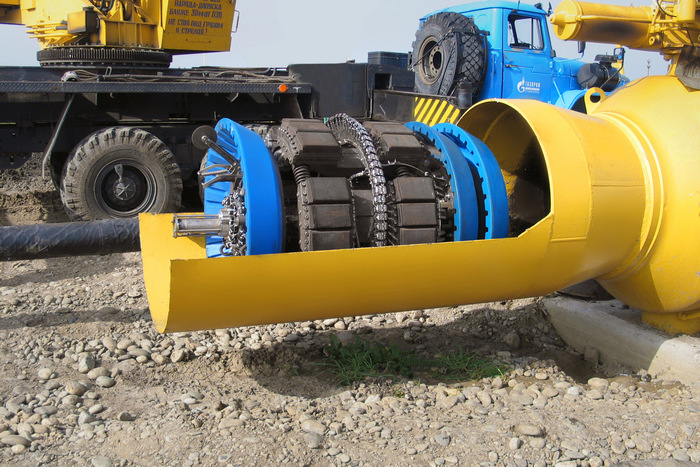
Here is a flaw detector. It can find the smallest defects in a gas pipeline.
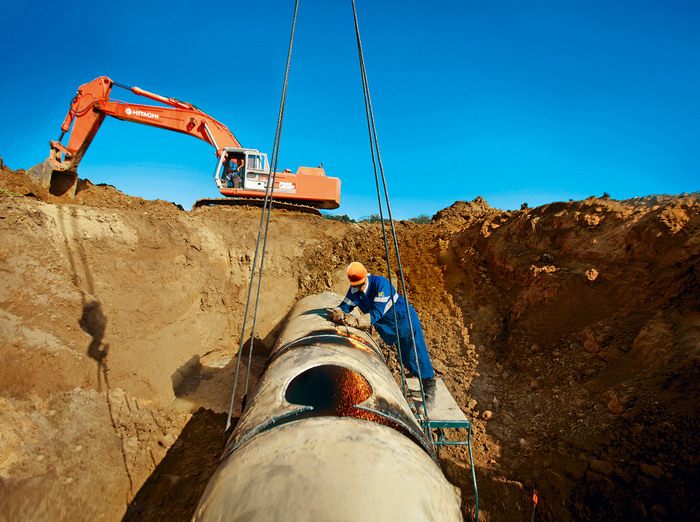
The planned launch of a flaw detector revealed anomalies on a weld at the 3.3 kilometer mark of the Northern Caucasus – Center gas pipeline in the Stavropol Territory. In order to resolve the problem, the gas pipeline was shut down and operations for replacing a defective pipe segment started. Such work is assigned to the most experienced specialists. Photo: electric and gas welder Vladimir Ovsyannikov – this year’s winner of the Best in Profession contest at the Izobilnenskoye Gas Line Pipe Operation Center.
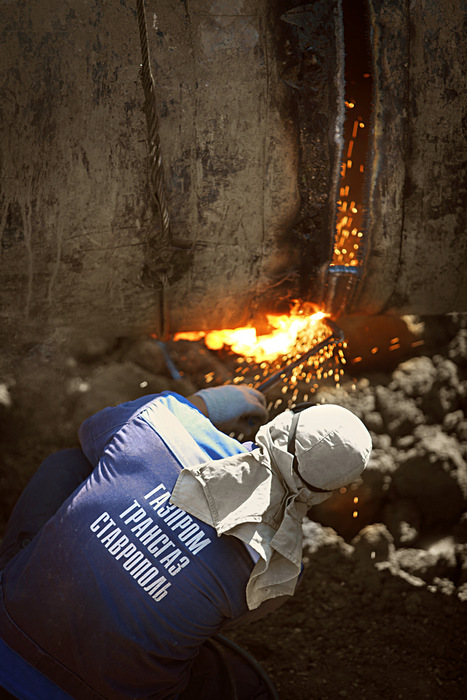
In order to remedy the defect, the respective segment of the pipe (the so-called spool) is removed and a new one is welded in its place. The diameter of the replaced pipe is 1,220 millimeters, the wall thickness – 12.4 millimeters. The gas workers have only 36 hours to do the entire scope of work.
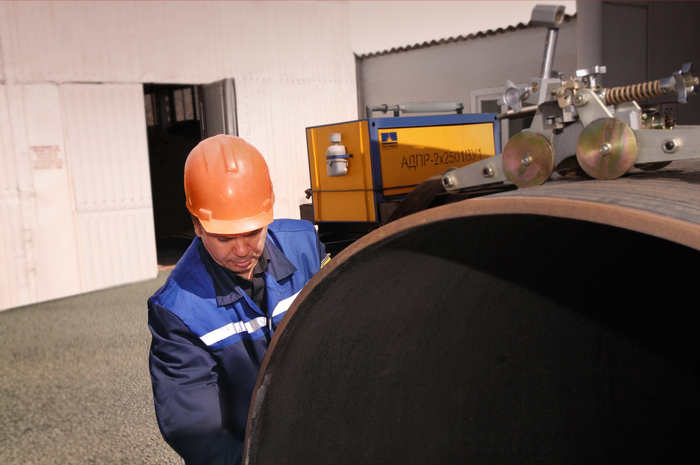
Under steady-state conditions a new pipe spool is prepared using the orbital cutting device. Electric and gas welder Vladimir Demidkin attaches the device to the pipe for cutting a piece that would be equal in size to that of the replaced segment.
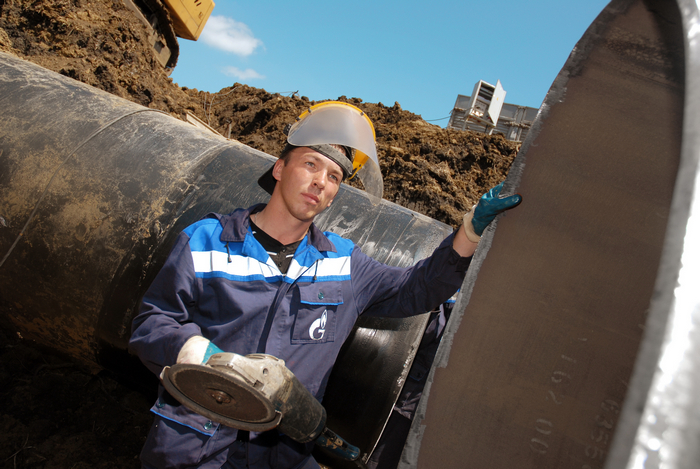
Before installing the new spool into the gas pipeline, Artyom Artouz, pipe fitter of the line pipe maintenance service, carefully treats its edges to ensure a perfect weld seam.
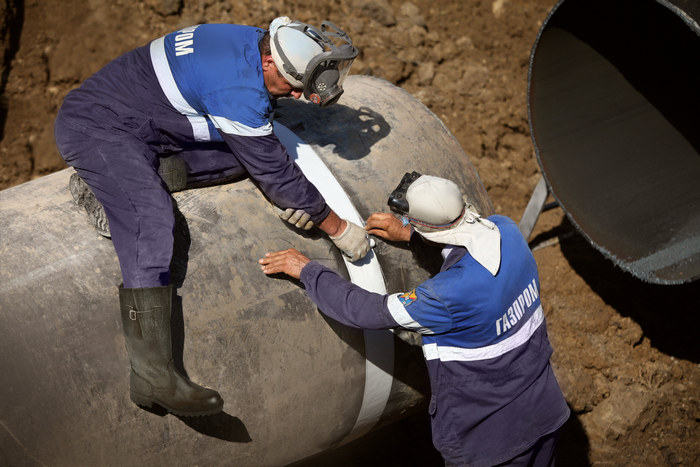
Hot works are underway. The new spool will be installed soon. Photo: Vladimir Ovsyannikov (near the pipe) and pipe layer Sergey Poddenezhny (on the pipe) – this year’s winner of the Best in Profession contest at Gazprom Transgaz Stavropol.
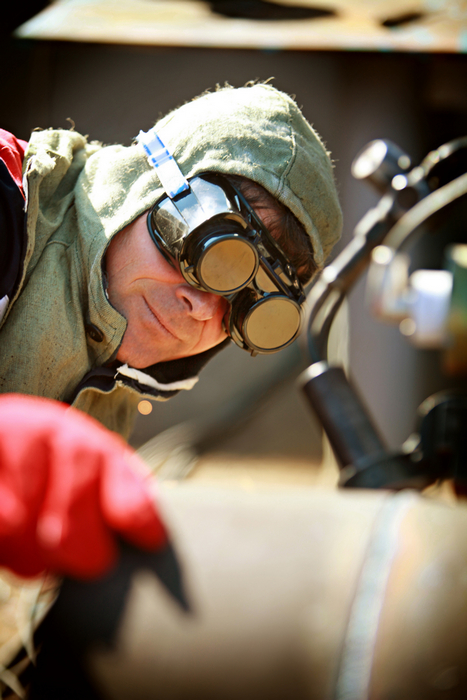
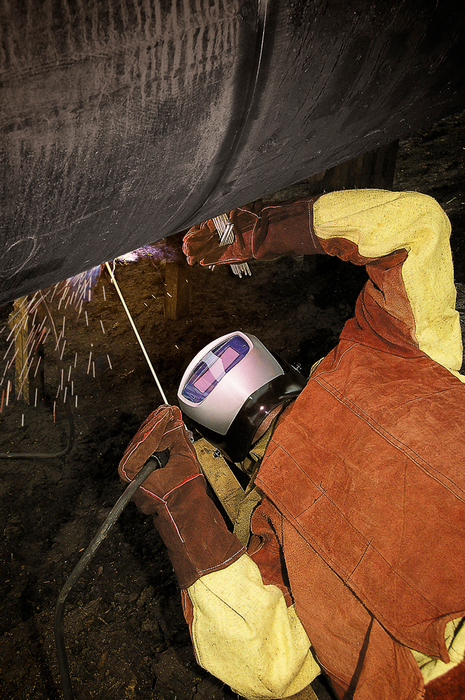
As you can see, safety assurance is an immutable rule in the gas industry. Working clothes of electric and gas welders are made of antistatic, fire-resistant fabrics with oil and water proofing. Special masks or glasses protect eyes during welding operations. Both photos: Alexey Nikulin, a multiple prize winner of contests among electric and gas welders from Gazprom Transgaz Stavropol and a prize winner of Gazprom’s contest.
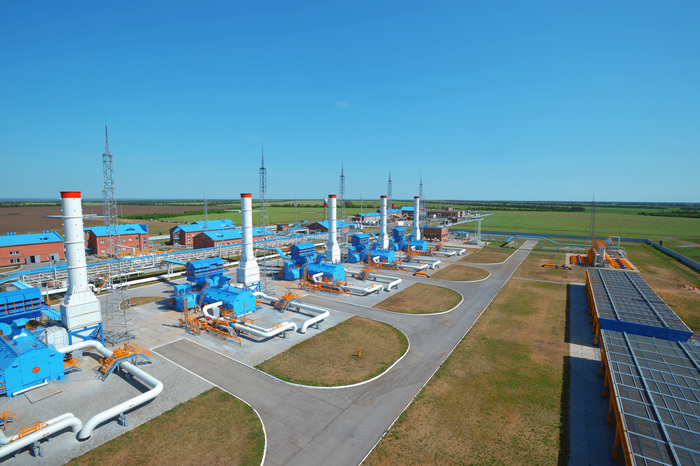
At the end of our trip along gas pipelines we will visit the Salskaya compressor station in the Rostov Region. Compressor stations are another crucial element of the gas transmission system, which have great significance for the ‘blue fuel’ supplies to consumers. Such stations are placed along gas pipelines with an interval of 100 kilometers. They secure a required pressure in the pipe, or, in other words, pump natural gas.
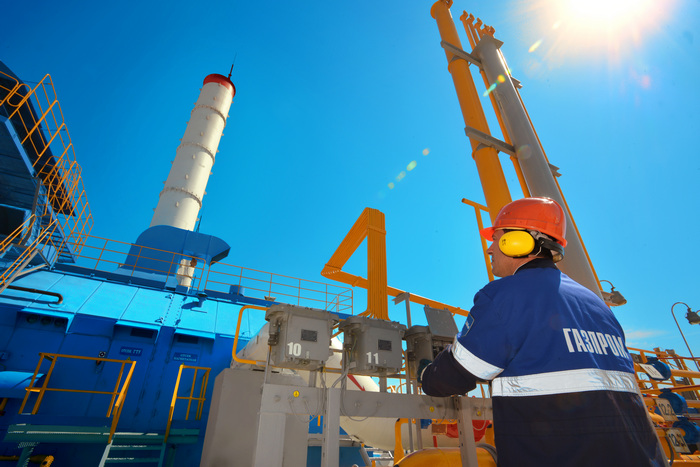
A gas compressor unit is the main equipment of a compressor station.
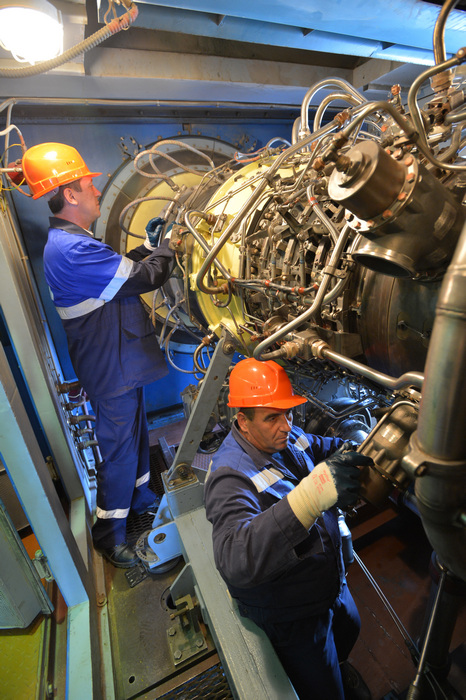
In the photo above, the maintenance of aircraft engine PS-90 is in progress.
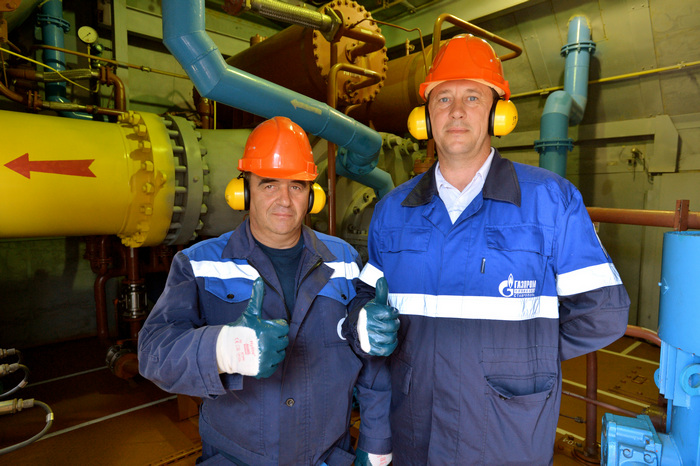
Everything is fine! The compressor station equipment is ready for the heating season.
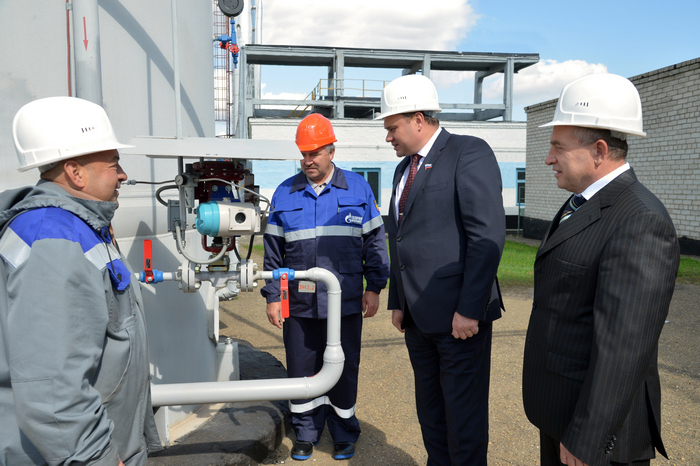
Director General of Gazprom Transgaz Stavropol Alexey Zavgorodnev (second from right) was inspecting the compressor station just in the time of our visit and was satisfied with the state of the facility.
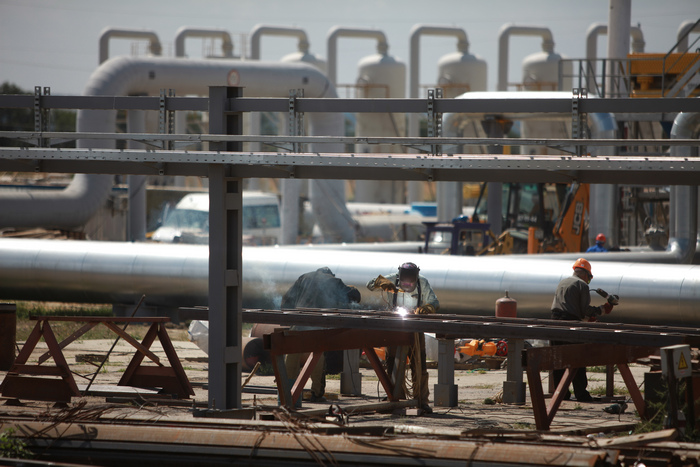
Now, let’s transport ourselves to another site of activities. In order to ensure uninterrupted gas supply to consumers during the winter period, it is important to have not only properly operating gas pipelines and compressor stations, but also backup gas at hand. This backup gas helps shave peak loads on the gas transmission system in the coldest days when gas consumption sharply increases. In southern Russia such gas is stockpiled in the Severo-Stavropolskoye underground gas storage (UGS) facility. As of September 27, 2013, more than 9 billion cubic meters of gas is injected into it. Right now, the retrofit of auxiliary equipment is nearing completion at booster compressor station No. 1 (BCS-1) – the region’s most powerful BCS servicing Severo-Stavropolskoye.

The scope of work is great. However, BCS-1 will be fully operational by the heating season start. As we can see in the photo above, a representative of the manufacturing plant (Frunze Sumy Engineering Works) is repairing the blowers of a gas compressor unit at BCS-1.
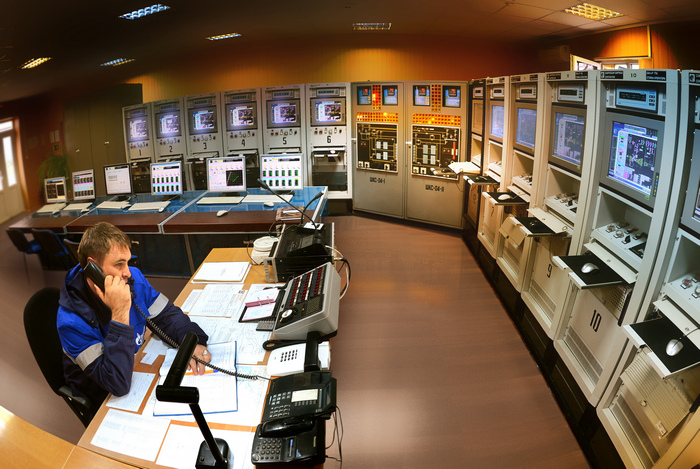
The control room is the heart of a booster compressor station. Shift engineer Alexey Mametyev is telling a dispatcher the parameters of gas injection into the UGS facility.
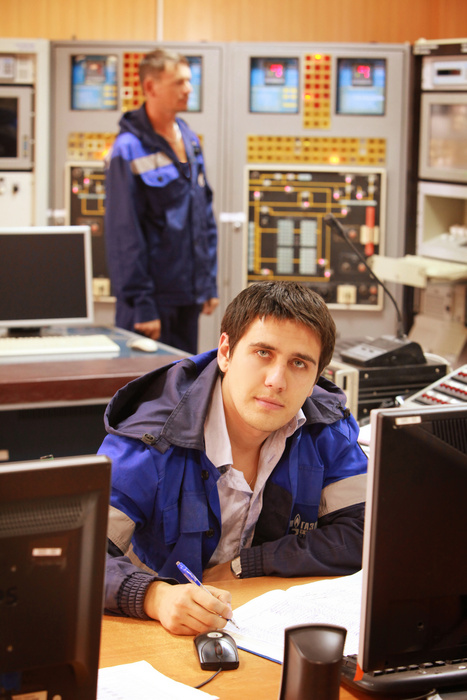
Engineer Stanislav Zhulin is responsible for smooth performance of the station and controls the operating mode of gas compressor units in order to timely correct a failure if necessary.
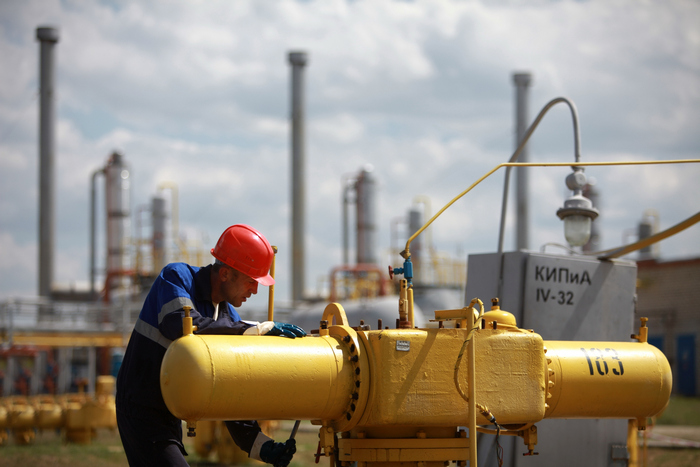
During a routine inspection of BCS-1 equipment Evgeny Spetsev, process unit operator, detected a hydraulic fluid leakage from the pneumohydrodrive of a ball valve and fixed the problem at once.
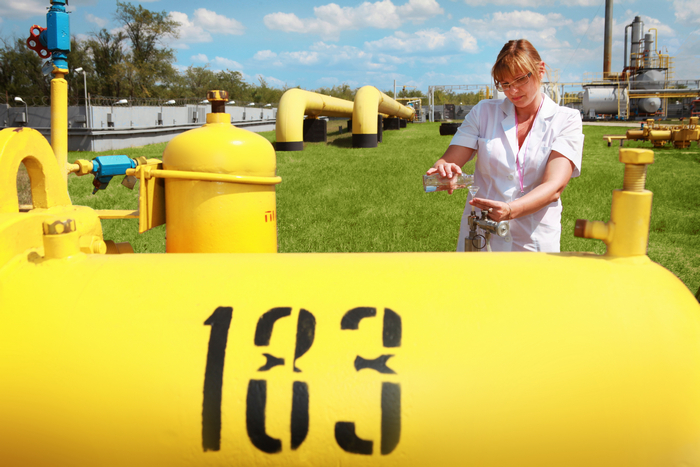
BCS-1 chemistry lab assistant Elena Bronnikova is preparing the Karpov absorption device to measure the content of water vapors and moisture dew-point in gas. Consumers should receive gas of proper quality.
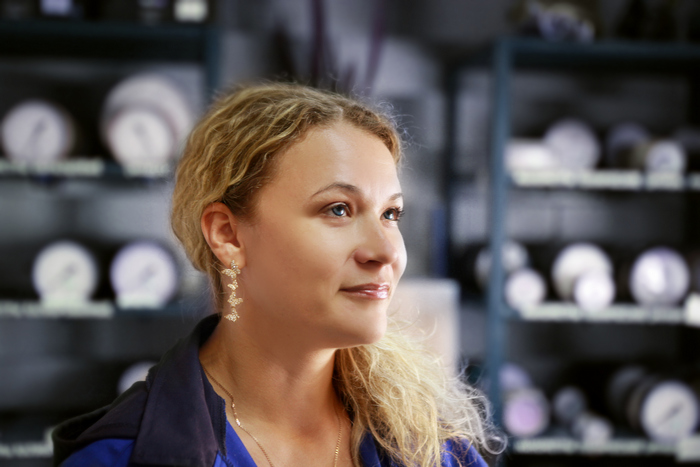
Svetlana Kuznetsova has several hundred gauges, each with specific testing time. Gauge calibration requires responsible attitude as its quality considerably influences the performance of the entire booster compressor station.
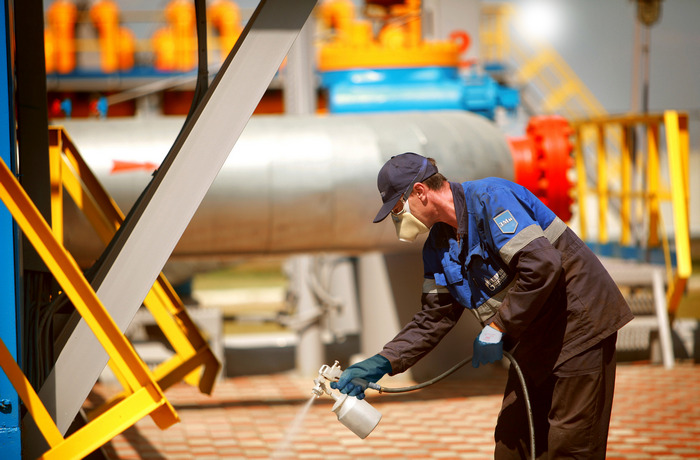
“Beauty will save the world” and will also protect against corrosion and destruction. Compressor operator Danil Ivanov is doing his best not so much for the beauty, but mostly for the business.
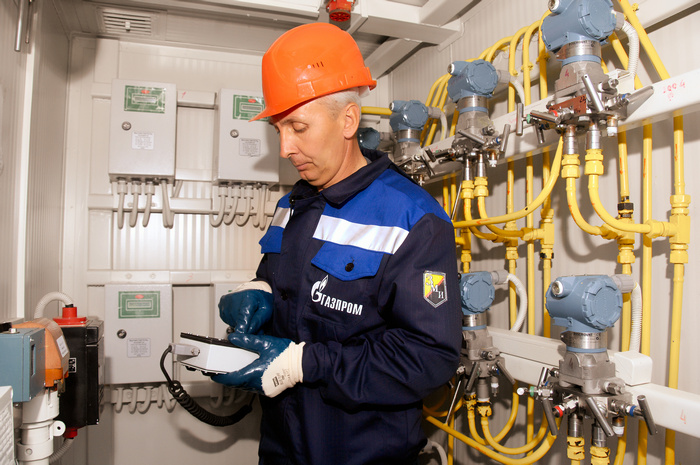
At the end of our photo essay, let’s pay a short visit to two gas distribution stations (Gazprom Transgaz Stavropol operates more than 300 such stations). The process parameters control is an integral part of the workflow at this crucial element of the gas transmission system. Operator Oleg Dutov is reading data from gas flow computers Superflow – IIE at the Krasnogvardeyskaya gas distribution station.
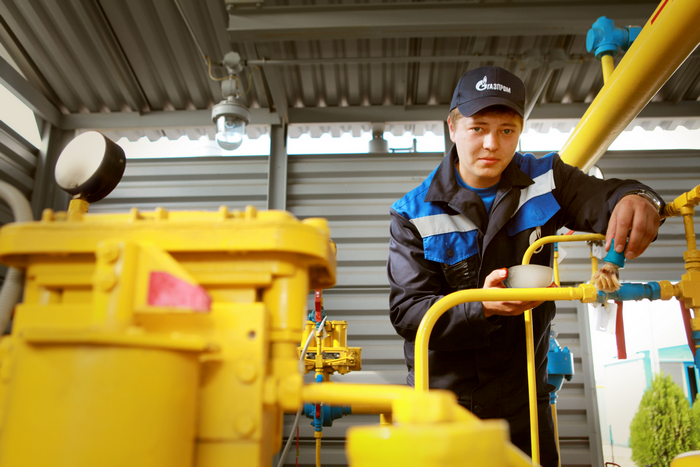
A gas leak is a dangerous signal. In order to check the leak tightness of connecting nodes, gas workers regularly conduct the so-called soap bubble test. Operator Vitaly Shevchenko is checking impulse line valves at a gas distribution station near the village of Pelagida in the Stavropol Territory.
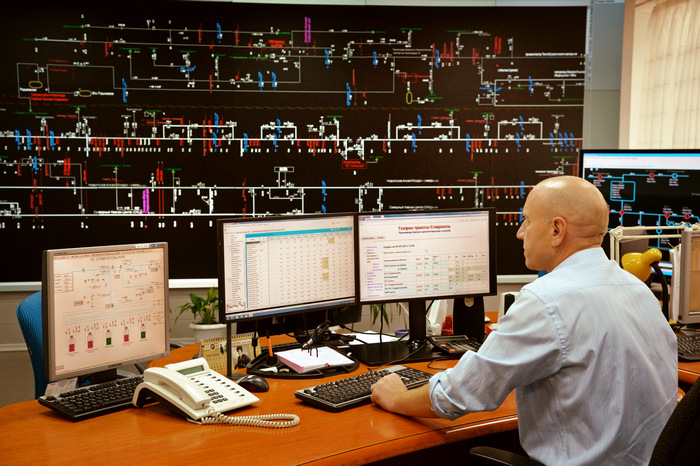
Our study trip ends at the operations and dispatch control service (ODCS) of Gazprom Transgaz Stavropol. The service exercises control over the gas supply system. Here we make sure once again that Stavropol gas workers hold everything in check and responsibly prepare for winter. Consumers can be confident – the gas transmission system will work trouble free. If there is gas, there is heat! Photo: ODCS shift supervisor Nikolai Kravchenko overseeing the gas transmission process.